Air Leakage Testing: Methods, Advantages and Comparisons
Leak testing is essential in the mass production of automotive and gas equipment components, ensuring quality, safety and efficiency in the final products. Traditionally, these processes have been bottlenecks due to the use of manual methods, such as bubble testing by water immersion.
However, today there are more advanced solutions such as air leak testing machines.
What are leak tests and why are they important?
Leak testing consists of identifying possible air or gas leaks in sealed products or components. This process is crucial to ensure that the product meets the required safety and quality specifications. Traditional methods, such as water immersion testing, have limitations such as human error and the inability to automate.
Modern testers, such as differential pressure systems, offer a more accurate, automated and cost-effective alternative for leak detection.
Advantages of Air Leak Testers
Automation and labor savings
- Fully automated processes.
- Less dependence on manpower.
- No specialized skills required for operation.
- Facilitates a safer and cleaner work environment.
- Easy maintenance.
Improved product quality
- Increases the accuracy and sensitivity of leak testing.
- Allows quantified specifications for leakage.
- Decreases product defect rates.
- Facilitates statistical analysis of test data.
Reduction of operating costs
- Lower rate of defective products and returns.
- Improves testing efficiency and speed.
- Eliminates additional processes, such as drying.
- Significant savings in long-term operating costs.
Leak Testing Methods: Comparison
Feature | Air leak testers | Water-dunk test, Bubble test |
Automation | High | Low |
Workload | Low | High |
Data management | Data management possible, Improves test performance | Not available |
Requires subsequent drying | No | Yes |
Types of leak detection methods
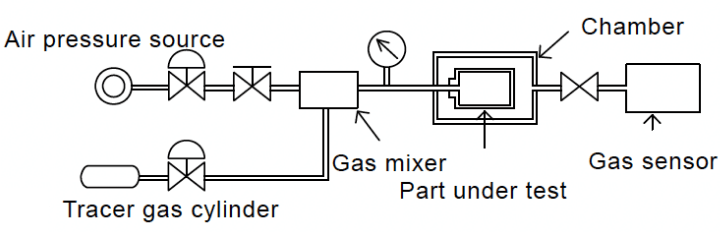
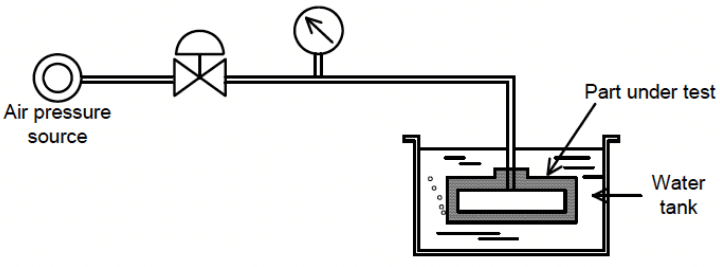
Water-dunk test, Bubble test
Pressurized air is sealed inside the work, and the work is then immersed in water or coated with soapy water to visually check air bubbles.

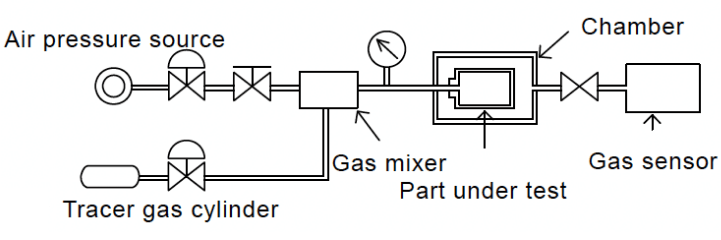
Tracer gas leak test
A gas (hydrogen, helium gas, organic halogen gas or chlorofluorocarbon gas) not present in the air is mixed with compressed air and sealed inside the work as a tracer gas to detect the gas leaking into the sealed container (chamber) containing the work with a gas detector (hydrogen leak detector, helium leak detector, etc. ).
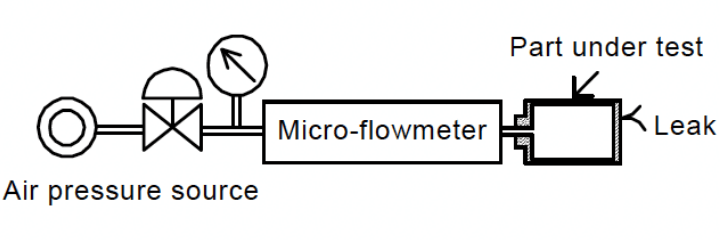
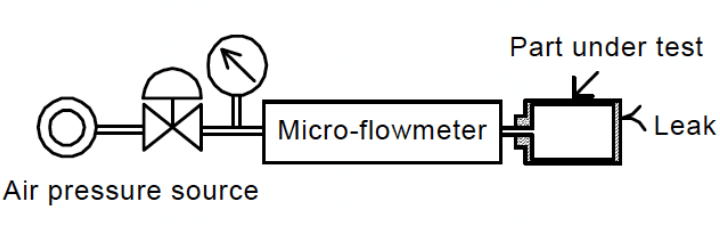
Flow measurement
Since the leak rate is equal to the flow rate, the leak can be measured by feeding air into the work through a micro flow meter.
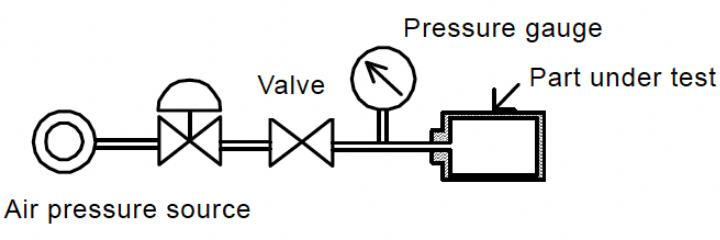
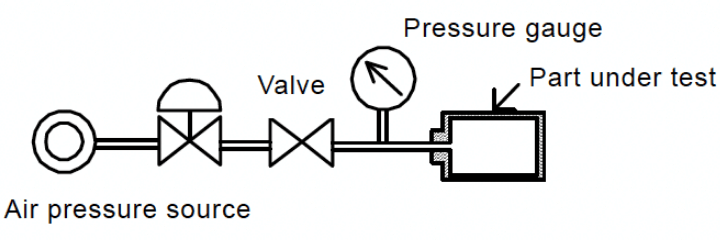
Pressure decay method, Vacuum decay method
Positive or vacuum pressure is applied. The pressure drop over time due to leak after sealing with a valve is then detected by a pressure gauge, pressure sensor, or pressure switch.
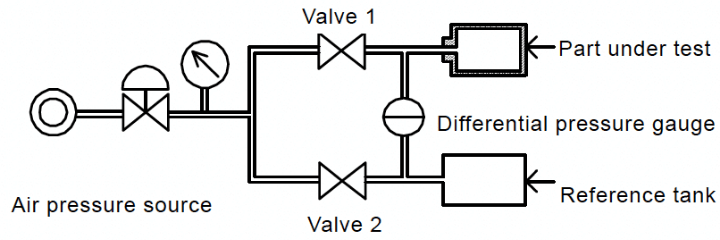
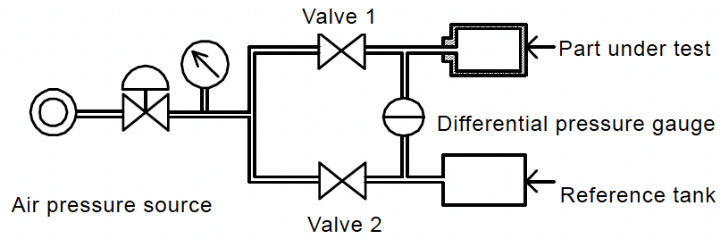
Differential pressure method
This method uses a differential pressure gauge (U-tube, differential pressure sensor, etc.) instead of a pressure gauge to detect the pressure drop due to leak as a differential pressure with the master tank with high sensitivity.
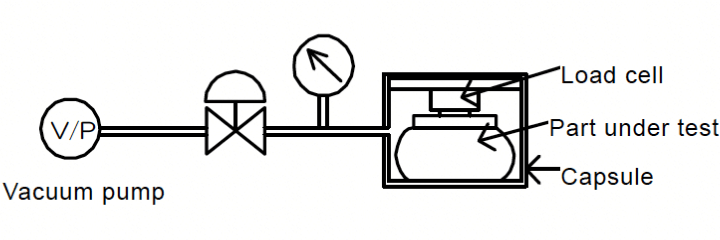
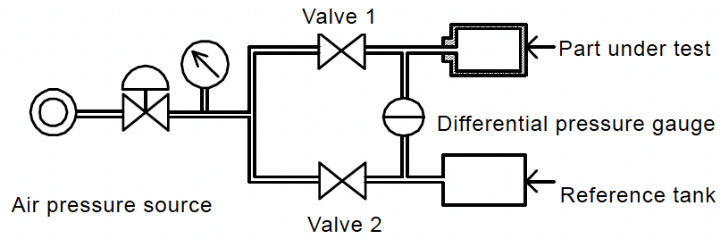
Distortion detection method
This method is used for packaged goods such as confectionery and medicines (e.g., pillow packaging). When a package containing air is placed in a capsule and the inside of the capsule is evacuated, the package expands, but if the package has a leak, it does not expand. The expansion is detected as distortion.
Why choose air leak testers?
Air leak testers are an advanced and efficient solution that replaces traditional methods. Offering accurate results, cost reduction and ease of automation, they are ideal for industries that prioritize quality and resource optimization.
If you are looking for reliable leak testing solutions for your production processes, differential pressure air testers are the most effective choice.